Getting vibrant plastisol prints on dark garments can be a challenge – but you can overcome it!
You can use special high-opacity plastisol inks for vibrant prints, but they can be expensive and difficult to print through fine mesh, giving your prints a heavy hand that can be uncomfortable. What’s the alternative? Printing an underbase.
What’s an Underbase and When Should You Use It?
What’s an underbase? It’s like a primer you’d use to prepare a surface before painting. By putting down a layer of white or light grey ink first, you can print other colors on top without losing vibrancy to the darker-colored garment underneath. If you’re not using high-opacity inks, you’ll probably need an underbase for most prints on anything other than white, pastel or other very light-colored garments. A possible exception is if you’re going for a washed-out, “vintage” look.
Screen Printing Your Underbase: Not as Easy as It Seems!
Screen printing an underbase isn’t quite as simple as just putting down a layer of white ink in the shape of your artwork. You’ll have to flash cure the underbase before you print colors on top of it. This means you’ll need a press with enough print heads to accommodate the underbase, flash cure and additional colors. For example, if you’ve got a two-color job that requires an underbase, your press will need at least four print heads. Printing an underbase also means your production will be slower compared to a job you wouldn’t have to flash cure – take this into account when you plan your turnaround time. If you want, you can charge for printing an underbase the same as you would any additional color.
Give Yourself a Good Foundation
When you print your underbase, you’ll want to use the least amount of ink possible for a soft hand, while still giving yourself a good foundation for the rest of the colors. Use a lower mesh count for your underbase than for your top colors, but not so low that you end up with rough texture. You want as smooth a base as possible. The right mesh count depends on your ink and the press you’re using, but in general 125-150 is a good place to start when printing underbases for spot color jobs. Use higher mesh counts (200+) for your underbase if you need to capture fine details or halftones. If your design has white in it, you should use a separate white for the underbase and top color. Using your white underbase as a highlight color uses too much ink, making the final print too thick and difficult to cure.
Keep Tight Registration with the Right Equipment
Tight registration is key to printing an underbase. Unless your design calls for a white outline, your underbase shouldn’t show up in the final print. When you set up your artwork, make the underbase a point or two skinnier than your top colors – this is called “choke” and it keeps your underbase inside the boundaries of the top layers of ink. This isn’t quite as easy as reducing the size of the underbase. Unless your design is symmetrical in all directions, it should be done with outlines to preserve the appearance of the artwork. It helps to have a high-quality, professional-grade screen printing machine to properly align the underbase and top colors, and you’ll also need well tensioned screens.
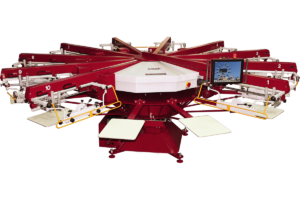
The all-electric Anatol VOLT screen printing machine uses servo motors for the smoothest operation possible, keeping your registration rock solid.
With the right technique and the right screen printing equipment, you can get brilliant plastisol prints even on dark garments. Screen printing underbase can be tricky, but like any other printing challenge, you can overcome it with practice! And don’t let your press hold you back – if you’re having trouble holding tight registration with your current equipment, let’s talk about how Anatol technology can make getting great results easier than ever.